When it comes to 3D printing, the sky is the limit. As 3D printing technology continues to advance, applications can be as far reaching as airplane and automobile parts to medical devices and even anatomically correct, biocompatible models. Although 3D printing technology is developing at a rapid pace, the technology itself is not new. It emerged in the 1980s as a means of creating rapid prototypes. In recent years the applications for 3D printed models have evolved with the available hardware, software, and printable materials. Evolving technology, paired with the creative and innovative minds of scientists, engineers, and physicians, has been the launching pad for developments within 3D printing technology specific to healthcare. One way 3D printing technology is poised to create better patient outcomes is in creating an anatomically and patient-specific models to aid in surgery and medical procedures. With the capability to 3D ...
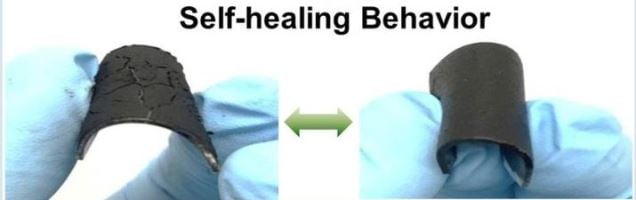
If your car has more scratches on it than the floor of a chicken coop, a new type of polymer may be just right for you. Researchers in the U.S. and Switzerland recently described a new class of polymer-based material that heals itself with light from a dentist’s lamp.
These polymers, called “metal lo supramolecular polymers”, turn into liquid to fill crevasses and gaps left by scratches when ultraviolet light is shone on them for less than a minute. When the light goes off, the polymers solidify again.
The researchers came from three different teams to create these self-healing polymers: Ohio’ s Case Western Reserve University group led by Stuart J. Rowan; the team at the University of Fribourg in Switzerland, led by Christoph Weder; and the Army Research Laboratory at Aberdeen Proving Ground‘s group in Maryland, led by Rick Beyer.
Lisa-Joy Zgorski at the National Science Foundation, which funded the work, explains:
The scientists envision widespread uses in the not-so-distant future for re-healable materials like theirs, primarily as coatings for consumer goods such as automobiles, floors and furniture. While their polymers are not yet ready for commercial use, they acknowledge, they now have proved that the concept works. And with that, what happens next is up to the market place. Necessity, the mother of invention, will expand the possibilities for commercial applications.
The polymers were created by a mechanism known as supramolecular assembly. Regular polymers are long, chain-like molecules with thousands of atoms. The metal lo supramolecular polymers, as shown in the YouTube video embedded above, were made of smaller molecules. Metal ions link the molecules together and turned them into longer, polymer-like chains.
When the intense ultraviolet light hit these metal lo supramolecular polymers, the assembled structures became temporarily unglued and turned from a solid into a liquid. The liquid flowed to fill in any openings. When the light was switched off, the material re-assembled into a solid coat with its properties intact.
Comments
Post a Comment